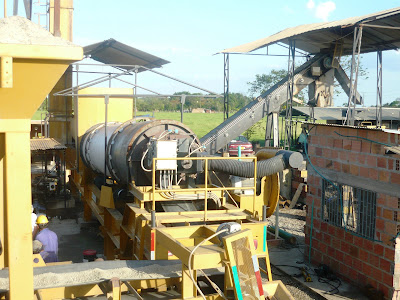
Bienvenidos
En mi blog podras encontrar informacion basica relacionada con procesos de soldadura, codigos y normas; ademas de seguridad industrial.
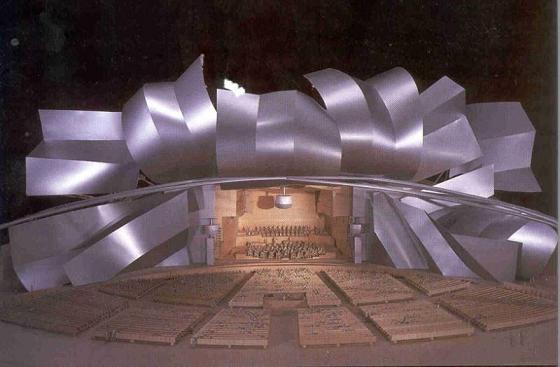
25/2/09
Suscribirse a:
Enviar comentarios (Atom)
Que significa la sigla SAW?
Introduccion
Existen muchos procesos de soldadura, la soldadura esta relacionada con casi todas las actividades, además de ser una importante industria en sí misma.
La tecnología de la soldadura se basa en el pensamiento original, tal como en muchas otras disciplinas científicas.
El crecimiento de esta rama de la ingeniería se realizó gracias a las contribuciones de hombres Comunes, hombres que no dudaron en aplicar cada pizca de conocimiento adquirido, cuando era posible, para resolver problemas prácticos.
LA SOLDADURA
¿Que es soldar? }
Soldar es el proceso de unir o juntar metales, ya sea que se calientan las piezas de metal hasta que se fundan y se unan entre sí o que se calienten a una temperatura inferior a su punto de fusión y se unan o liguen con un metal fundido como relleno.
Otro método es calentarlas hasta que se ablanden lo suficiente para poder unirlas con un martillo a presión.
HISTORIA DE LA SOLDADURA
Es difícil obtener una relación exacta del perfeccionamiento de la soldadura y de las personas que participaron, porque se estaban efectuando muchos experimentos y técnicas de soldadura en diferentes países y al mismo tiempo.
Aunque en el trabajo; los metales y la unión de los mismos datan de hace siglos, tal parece que la soldadura, tal como la conocemos en la actualidad, hizo su aportación alrededor del año 1900.
La historia de la soldadura no estaría completa sin mencionar las contribuciones realizadas por los antiguos metalúrgicos.
Existen manuscritos que detallan el hermoso trabajo en metales realizados en tiempos de los Faraones de Egipto, en el Antiguo Testamento el trabajo en metal se menciona frecuentemente.
En el tiempo del Imperio Romano ya se habían desarrollado algunos procesos, los principales eran soldering, brazing y la forja.
La forja fue muy importante en la civilización romana es así como a Vulcano, dios del fuego, se le atribuía gran habilidad en este proceso y otras artes realizados con metales.
TIPOS DE MÁQUINAS PARA SOLDAR
Soldadoras rectificadoras p/arco de 500 amp.
Soldadoras rotativas de 20 HP. - 500 amp.
Soldadora para punto.
Soldadora sistema Tig. 350 amp.para soldar aluminio, bronce, cobre y acero inoxidable.
Soldadora Mag-Mig. para hierro, acero inoxidable y aluminio.
CONCLUCION
La tecnología y la ciencia de la soldadura han avanzado con tal rapidez en los últimos años, que sería casi imposible enumerar todos los métodos diferentes de soldadura que actualmente están en uso. Sin embargo, todos en dos categorías diferentes: soldadura por fusión y soldadura sin fusión.
Gracias al desarrollo de nuevas técnicas se ha logrado notar que durante la primera mitad del siglo XX, la soldadura sustituyó al atornillado y al remachado en la construcción de muchas estructuras, como puentes, edificios y barcos.
La tecnología de la soldadura se basa en el pensamiento original, tal como en muchas otras disciplinas científicas.
El crecimiento de esta rama de la ingeniería se realizó gracias a las contribuciones de hombres Comunes, hombres que no dudaron en aplicar cada pizca de conocimiento adquirido, cuando era posible, para resolver problemas prácticos.
LA SOLDADURA
¿Que es soldar? }
Soldar es el proceso de unir o juntar metales, ya sea que se calientan las piezas de metal hasta que se fundan y se unan entre sí o que se calienten a una temperatura inferior a su punto de fusión y se unan o liguen con un metal fundido como relleno.
Otro método es calentarlas hasta que se ablanden lo suficiente para poder unirlas con un martillo a presión.
HISTORIA DE LA SOLDADURA
Es difícil obtener una relación exacta del perfeccionamiento de la soldadura y de las personas que participaron, porque se estaban efectuando muchos experimentos y técnicas de soldadura en diferentes países y al mismo tiempo.
Aunque en el trabajo; los metales y la unión de los mismos datan de hace siglos, tal parece que la soldadura, tal como la conocemos en la actualidad, hizo su aportación alrededor del año 1900.
La historia de la soldadura no estaría completa sin mencionar las contribuciones realizadas por los antiguos metalúrgicos.
Existen manuscritos que detallan el hermoso trabajo en metales realizados en tiempos de los Faraones de Egipto, en el Antiguo Testamento el trabajo en metal se menciona frecuentemente.
En el tiempo del Imperio Romano ya se habían desarrollado algunos procesos, los principales eran soldering, brazing y la forja.
La forja fue muy importante en la civilización romana es así como a Vulcano, dios del fuego, se le atribuía gran habilidad en este proceso y otras artes realizados con metales.
TIPOS DE MÁQUINAS PARA SOLDAR
Soldadoras rectificadoras p/arco de 500 amp.
Soldadoras rotativas de 20 HP. - 500 amp.
Soldadora para punto.
Soldadora sistema Tig. 350 amp.para soldar aluminio, bronce, cobre y acero inoxidable.
Soldadora Mag-Mig. para hierro, acero inoxidable y aluminio.
CONCLUCION
La tecnología y la ciencia de la soldadura han avanzado con tal rapidez en los últimos años, que sería casi imposible enumerar todos los métodos diferentes de soldadura que actualmente están en uso. Sin embargo, todos en dos categorías diferentes: soldadura por fusión y soldadura sin fusión.
Gracias al desarrollo de nuevas técnicas se ha logrado notar que durante la primera mitad del siglo XX, la soldadura sustituyó al atornillado y al remachado en la construcción de muchas estructuras, como puentes, edificios y barcos.
SIMBOLOS DE SOLDADURA
Tenemos muchos símbolos en nuestra sociedad tecnológica. Tenemos señales y rótulos que nos dicen lo que debemos hacer y dónde ir o lo que no debemos hacer o dónde no ir. Las señales de transito son un buen ejemplo. Muchas de estas señales les ya son de uso internacional no requieren largas explicaciones y, con ellas, no hay la barrera del idioma, porque cualquier persona los puede interpretar aunque no conozcan ese idioma. En la soldadura, se utilizan ciertos signos en los planos sé ingeniería para indicar al soldador ciertas reglas que deben seguir, aunque no tenga conocimientos de ingeniería. Estos signos gráficos se llaman símbolos de soldadura. Una vez que se entiende el lenguaje de estos símbolos, es muy fácil leerlos.
Símbolos de soldadura
Los símbolos de soldadura se utilizan en la industria para representar detalles de diseño que ocuparían demasiado espacio en el dibujo si estuvieran escritos con todas sus letras. Por ejemplo, el ingeniero o el diseñador desea hacer llegar la siguiente información al taller de soldadura:
El punto en donde se debe hacer la soldadura.
Que la soldadura va ser de filete en ambos lados de la unión.
Un lado será una soldadura de filete de 12 mm; el otro una soldadura de 6mm.
Ambas soldaduras se harán un electrodo E6014.
La soldadura de filete de 12mm se esmerilará con máquina que desaparezca
Para dar toda esta información, el ingeniero o diseñador sólo pone el símbolo en el lugar correspondiente en el plano para trasmitir la información al taller de soldadura
Los símbolos de soldadura son tan esenciales en el trabajo del soldador como correr un cordón o llenar una unión. La American Welding Society (AWS) ha establecido un grupo de símbolos estándar utilizados en la industria para indicar e ilustrar toda la información para soldar en los dibujos y planos de ingeniería.
PARTES DEL SÍMBOLO DE SOLDADURA
1) La línea de referencia siempre será la misma en todos los símbolos. Sin embargo, si el símbolo de soldadura está debajo (sig figura) de la línea de referencia, la soldadura se hará en el lado de la unión hacia el cual apuntara la flecha. Si el símbolo de la soldadura está encimada de la línea de referencia, la soldadura se hará en el lado de la unión, opuesto al lado en que apunta la flecha
2) La flecha puede apuntar en diferentes direcciones y, aveces, puede ser quebrada (Sig. figura)
3) Hay muchos símbolos de soldadura, cada uno correspondiente a una soldadura en particular.
4) Se agregan acotaciones (dimensionales) adicionales a la derecha del símbolo si la unión se va a soldar por puntos en caso de la soldadura de filete. La primera acotación adicional en la (Sig. fig.) indica la longitud de la soldadura; la segunda dimensional indica la distancia entre centros de la soldadura.
5) La cola quizá no contenga información especial y a veces, se pueda omitir.
6) Hay una gran variedad de símbolos complementarios, cada uno un signo deferente.
Combinación de símbolos y resultados
Algunos símbolos son muy complicados o parecen serlo a primera vista; pero si se estudian punto por punto, no son difíciles de entender. El primer punto que se observa en la figura (sig figura) es la parte del símbolo que indica doble chaflán (bisel) o doble V. Los chaflanes dobles, o doble V, se preparan en una sola de las piezas de metal, de modo que el trabajo se hará como se muestra acontinuación:
A continuación está el símbolo de soldadura de filete en ambos lados de la línea de referencia. Pero antes de poder aplicar una soldadura de filete, debe haber una superficie vertical. Por tanto, se rellena el chaflán con soldadura como se ve en la siguiente figura.
Después de rellenar los chaflanes, se aplica la soldadura.. Esta combinación es poco común y rara vez se usa. Sólo se aplica en donde se requiere resistencia y penetrancia del 100%. Sin embargo, se ha utilizado como ejemplo para mostrar los pasos en la lectura de símbolos. Hay gran número de combinaciones que se pueden utilizar, pero los símbolos básicos de soldadura y los símbolos completamente mostrados en la sig. Figura. Acabaron la mayor parte de ellas.
APLICACIONES DE LOS SÍMBOLOS DE SOLDADURA
En las figuras anteriores se muestran los símbolos muy básicos para soldar y sus aplicaciones. Pero se debe recordar que son simples ilustraciones y que probablemente incluirá mucha más información si fuera parte de un plano real.
PUNTOS QUE DEBEMOS RECORDAR
Los símbolos de soldadura en los dibujos y planos de ingeniería representan detalles de diseño.
Los símbolos de soldadura se utilizan en lugar de repetir instrucciones normales.
La línea de referencia no cambia.
La flecha puede apuntar en diferentes direcciones.
En ocasiones, se puede omitir la cola del símbolo
Hay muchos símbolos, dimensiones (acotaciones) y símbolos complementarios.
Los símbolos no son complicados si se estudian punto por punto.
FACTORES PARA MANEJAR PROPIAMENTE EL PROCESO.
- Diámetro correcto del electrodo.
- Tipo de corriente apropiada
- Correcta selección cantidad de corriente (amperaje y voltaje).
- Correcta longitud de arco.
- Correcta velocidad de soldeo.
- Ángulos correctos de aplicación.
PUNTOS A VERIFICAR PARA LA CALIDAD EN SOLDADURA
1.- Use máquinas, electrodos y accesorios de calidad, Conozca el tipo y propiedades del metal basé.
2.- Seleccione el proceso adecuado para tener la mas alta calidad al soldar el metal base.
3.- Seleccione el procedimiento a emplear en base al uso final de la soldadura.
4.- Seleccione el electrodo correctamente en base a la junta a emplear.
5.- Limpie el material base de escorias, pintura, óxidos, grasas, etc.
6.- No soldé sobre fracturas o porosidad creadas por la soldadura anterior, primero remueva estas.
7.- Cuando la abertura de raíz sea muy grande primero repare esta.
8.- Ponga especial atención en el primer pase de penetración a raíz.
9.- Remueva la escoria del cordón depositado anteriormente hasta que vaya a realizar el pase siguiente sobre este. En caso de haber pase siguiente entonces hasta que este fría.
10.- Observe las dimensiones de la soldadura requerida y asegurase de obtener estas.
11.- Inspeccione su trabajo inmediatamente y remueva los defectos si los hay repárelos inmediatamente.
12.- Asegure que la apariencia de la soldadura sea la correcta si no repárese.
Símbolos de soldadura
Los símbolos de soldadura se utilizan en la industria para representar detalles de diseño que ocuparían demasiado espacio en el dibujo si estuvieran escritos con todas sus letras. Por ejemplo, el ingeniero o el diseñador desea hacer llegar la siguiente información al taller de soldadura:
El punto en donde se debe hacer la soldadura.
Que la soldadura va ser de filete en ambos lados de la unión.
Un lado será una soldadura de filete de 12 mm; el otro una soldadura de 6mm.
Ambas soldaduras se harán un electrodo E6014.
La soldadura de filete de 12mm se esmerilará con máquina que desaparezca
Para dar toda esta información, el ingeniero o diseñador sólo pone el símbolo en el lugar correspondiente en el plano para trasmitir la información al taller de soldadura
Los símbolos de soldadura son tan esenciales en el trabajo del soldador como correr un cordón o llenar una unión. La American Welding Society (AWS) ha establecido un grupo de símbolos estándar utilizados en la industria para indicar e ilustrar toda la información para soldar en los dibujos y planos de ingeniería.
PARTES DEL SÍMBOLO DE SOLDADURA
1) La línea de referencia siempre será la misma en todos los símbolos. Sin embargo, si el símbolo de soldadura está debajo (sig figura) de la línea de referencia, la soldadura se hará en el lado de la unión hacia el cual apuntara la flecha. Si el símbolo de la soldadura está encimada de la línea de referencia, la soldadura se hará en el lado de la unión, opuesto al lado en que apunta la flecha
2) La flecha puede apuntar en diferentes direcciones y, aveces, puede ser quebrada (Sig. figura)
3) Hay muchos símbolos de soldadura, cada uno correspondiente a una soldadura en particular.
4) Se agregan acotaciones (dimensionales) adicionales a la derecha del símbolo si la unión se va a soldar por puntos en caso de la soldadura de filete. La primera acotación adicional en la (Sig. fig.) indica la longitud de la soldadura; la segunda dimensional indica la distancia entre centros de la soldadura.
5) La cola quizá no contenga información especial y a veces, se pueda omitir.
6) Hay una gran variedad de símbolos complementarios, cada uno un signo deferente.
Combinación de símbolos y resultados
Algunos símbolos son muy complicados o parecen serlo a primera vista; pero si se estudian punto por punto, no son difíciles de entender. El primer punto que se observa en la figura (sig figura) es la parte del símbolo que indica doble chaflán (bisel) o doble V. Los chaflanes dobles, o doble V, se preparan en una sola de las piezas de metal, de modo que el trabajo se hará como se muestra acontinuación:
A continuación está el símbolo de soldadura de filete en ambos lados de la línea de referencia. Pero antes de poder aplicar una soldadura de filete, debe haber una superficie vertical. Por tanto, se rellena el chaflán con soldadura como se ve en la siguiente figura.
Después de rellenar los chaflanes, se aplica la soldadura.. Esta combinación es poco común y rara vez se usa. Sólo se aplica en donde se requiere resistencia y penetrancia del 100%. Sin embargo, se ha utilizado como ejemplo para mostrar los pasos en la lectura de símbolos. Hay gran número de combinaciones que se pueden utilizar, pero los símbolos básicos de soldadura y los símbolos completamente mostrados en la sig. Figura. Acabaron la mayor parte de ellas.
APLICACIONES DE LOS SÍMBOLOS DE SOLDADURA
En las figuras anteriores se muestran los símbolos muy básicos para soldar y sus aplicaciones. Pero se debe recordar que son simples ilustraciones y que probablemente incluirá mucha más información si fuera parte de un plano real.
PUNTOS QUE DEBEMOS RECORDAR
Los símbolos de soldadura en los dibujos y planos de ingeniería representan detalles de diseño.
Los símbolos de soldadura se utilizan en lugar de repetir instrucciones normales.
La línea de referencia no cambia.
La flecha puede apuntar en diferentes direcciones.
En ocasiones, se puede omitir la cola del símbolo
Hay muchos símbolos, dimensiones (acotaciones) y símbolos complementarios.
Los símbolos no son complicados si se estudian punto por punto.
FACTORES PARA MANEJAR PROPIAMENTE EL PROCESO.
- Diámetro correcto del electrodo.
- Tipo de corriente apropiada
- Correcta selección cantidad de corriente (amperaje y voltaje).
- Correcta longitud de arco.
- Correcta velocidad de soldeo.
- Ángulos correctos de aplicación.
PUNTOS A VERIFICAR PARA LA CALIDAD EN SOLDADURA
1.- Use máquinas, electrodos y accesorios de calidad, Conozca el tipo y propiedades del metal basé.
2.- Seleccione el proceso adecuado para tener la mas alta calidad al soldar el metal base.
3.- Seleccione el procedimiento a emplear en base al uso final de la soldadura.
4.- Seleccione el electrodo correctamente en base a la junta a emplear.
5.- Limpie el material base de escorias, pintura, óxidos, grasas, etc.
6.- No soldé sobre fracturas o porosidad creadas por la soldadura anterior, primero remueva estas.
7.- Cuando la abertura de raíz sea muy grande primero repare esta.
8.- Ponga especial atención en el primer pase de penetración a raíz.
9.- Remueva la escoria del cordón depositado anteriormente hasta que vaya a realizar el pase siguiente sobre este. En caso de haber pase siguiente entonces hasta que este fría.
10.- Observe las dimensiones de la soldadura requerida y asegurase de obtener estas.
11.- Inspeccione su trabajo inmediatamente y remueva los defectos si los hay repárelos inmediatamente.
12.- Asegure que la apariencia de la soldadura sea la correcta si no repárese.
PARTES DE UN PROCEDIMIENTO DE SOLDADURA
WPS: ESPECIFICACIÓN DEL PROCEDIMIENTO DE SOLDADURA (WELDING PROCEDURE SPECIFICATION)
PQR: REGISTRO DE LA CALIFICACIÓN DEL PROCEDIMIENTO (PROCEDURE QUALIFICATION RECORD)
3. WPQ: CALIFICACIÓN DE LA HABILIDAD DEL SOLDADOR U OPERARIO. (WELDER PERFORMANCE QUALIFICATION)
ESPECIFICACIÓN DEL PROCEDIMIENTO DE SOLDADURA (WPS)
DOCUMENTO PREPARADO POR UN DEPARTAMENTO TÉCNICO O DE INGENIERÍA DE LA EMPRESA PARA DAR INSTRUCCIONES PRECISAS AL PERSONAL QUE EJECUTA Y AL QUE INSPECCIONA LAS SOLDADURAS.
ESPECIFICACIÓN DEL PROCEDIMIENTO DE SOLDADURA (WPS)
EL PROPÓSITO DE UNA WPS ES DEFINIR Y DOCUMENTAR TODOS LOS DETALLES QUE SE DEBEN TENER EN CUENTA AL SOLDAR MATERIALES O PARTES ESPECÍFICAS.
CONTENIDO DE UNA WPS
SU CONTENIDO DEBE ESTAR DE ACUERDO CON:
ü LOS REQUERIMIENTOS APLICABLES DE LOS CÓDIGOS
ü DE LAS EXIGENCIAS DEL CONTRATO U ORDEN DE COMPRA Y
ü DE LAS BUENAS PRÁCTICAS DE INGENIERÍA
TODAS LAS VARIABLES ESENCIALES, RELATIVAS A CADA PROCESO DE SOLDADURA UTILIZADO.
2. TODAS LAS VARIABLES NO ESENCIALES, RELATIVAS A CADA PROCESO DE SOLDADURA UTLIZADO.
3. LAS VARIABLES ESENCIALES SUPLEMENTARIAS , CUANDO SE REQUIERAN PRUEBAS DE IMPACTO DE LA SOLDADURA.
4. INFORMACIÓN ADICIONAL QUE SE CONSIDERE NECESARIA PARA OBTENER LAS SOLDADURAS DESEADAS.
CONTENIDO DEL WPS
1. Identificación de la WPS, de la empresa y del responsable de la WPS.
2. Alcance.
3. Identificación de los metales base: Especificación, tipo y/o grado.
4. Proceso (s) de soldadura utilizados.
5. Diseño de la juntas, tolerancias y detalles.
6. Tipo, clasificación y composición de los metales de aporte y otros materiales de soldadura. También se pueden incluir las condiciones de almacenamiento de estos materiales.
7. Posiciones en las cuales es aplicable el procedimiento.
8. Precalentamiento y temperaturas entre pases.
9. PWTH
10. Tipo y composición de los gases de protección, cuado sea aplicable
11. Tipo de corriente eléctrica, polaridad y rangos de corriente para los diferentes tipos y tamaños de electrodos o varillas utilizadas
12. Voltaje y velocidad de avance del arco
13. Otras características eléctricas (modo de transferencia, velocidad de alimentación del alambre, etc.)
14. Preparación de las juntas y limpieza de las superficies para la soldadura
15. Puntos de soldadura para armado y ensamble de las partes
16. Preparación de la raíz de la soldadura antes de soldar por el otro lado
17. Entrada de calor a la junta
18. Otras como: tipo de cordón, boquillas de gas, oscilación, distancia de contacto del electrodo, simple o múltiples pases, martillado de las juntas y otros aspectos que se consideren relevantes
REGISTRO DE LA CALIFICACIÓN DEL PROCEDIMIENTO (PQR)
DOCUMENTO QUE VALIDA Y RESPALDA UNA WPS, EN EL CUAL SE REGISTRAN LOS VALORES REALES DE LAS VARIABLES DEL PROCEDIMIENTO DE SOLDADURA USADO PARA EJECUTAR UNA CALIFICACIÓN EN UNA PROBETA SOLDADA Y LOS VALORES DE LOS RESULTADOS OBTENIDOS DE LAS PRUEBAS Y ENSAYOS EFECTUADOS A LA MISMA.
¿PARA QUÉ SE EVALÚA UNA UNIÓN SOLDADA?
l DETECTAR, CARACTERIZAR Y EVALUAR LAS DISCONTINUIDADES
l DETERMINAR CUMPLIMIENTO CON EL DISEÑO
l CALIFICAR PROCEDIMIENTOS DE SOLDADURA
l CALIFICAR SOLDADORES, OPERARIOS Y PUNTEADORES
l EVALUAR COMPORTAMIENTO DE LA CONSTRUCCIÓN SOLDADA EN SERVICIO
¿QUÉ TIPO DE EVALUACIONES EXISTEN?
ENSAYOS DESTRUCTIVOS
l TENSIÓN
l DOBLAMIENTO GUIADO
l ROTURA NICK
l MACROATAQUE
l ROTURA DEL FILETE
l IMPACTO
ENSAYOS NO DESTRUCTIVOS (END)
l INSPECCIÓN VISUAL (VT)
l RADIOGRAFÍA (RT)
l ULTRASONIDO (UT)
l PARTÍCULAS MAGNÉTICAS (MT)
l LÍQUIDOS PENETRANTES (PT)
OBTENCIÓN DEL PQR
PQR = IV y/o END y ED
IV: Inspección Visual END: Ensayos No Destructivos ED: Ensayos Destructivos
OBTENCIÓN DEL WPQ
WPQ = IV y END
WPQ = IV y ED
IV: Inspección Visual END: Ensayos No Destructivos ED: Ensayos Destructivos
SECUENCIA DE UNA CALIFICACIÓN
WPS
EJECUCIÓN CUPÓN DE PRUEBA
VT (CRITERIOS DEL CÓDIGO)
END (cuando se requiera)
UBICACIÓN, IDENTIFICACIÓN, RAYADO Y ESTAMPE DE PROBETAS
EXTRACCIÓN Y MECANIZADO DE PROBETAS
EJECUCIÓN DE LOS RESPECTIVOS ENSAYOS
ANÁLISIS DE RESULTADOS (CRITERIOS DEL CÓDIGO)
INFORME: RECHAZO O CERTIFICACIONES (PQR; WPQ)
Arco submergido
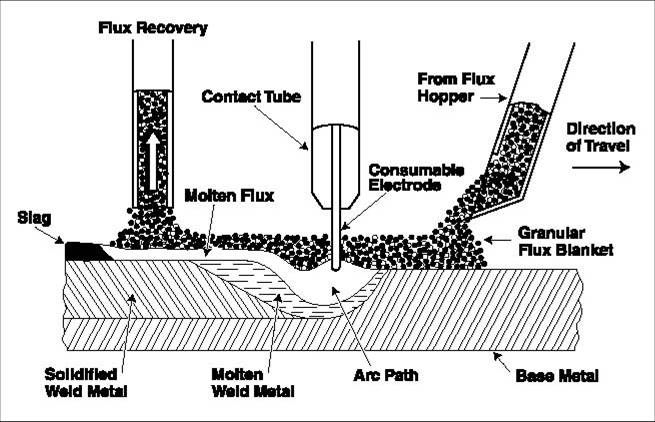
SAW
SOLDADURA POR ARCO SUBMERGIDO
SAW = Submerged Arc Welding
Es un proceso de soldadura por arco eléctrico que usa un arco (o varios) entre el electrodo y el charco de soldadura. El arco y el metal fundido son protegidos por una capa de fundente granular sobre el área de soldadura. El proceso no requiere presión y el material de aporte es el alambre (o alambres) el cual es el que hace el arco o se puede alimentar por otra fuente supplementaria.
El fundente.
Entre las principales funciones del fundente para la soldadura de arco sumergido podríamos enumerar las siguientes:
Ø Protege la soldadura fundida de la interacción con la atmósfera.
Ø Limpia y desoxida la soldadura fundida.
Ø Ayuda a controlar las propiedades químicas y mecánicas del metal de aporte en la soldadura.
Ø Existen dos métodos importantes para elaborar los fundentes, Granulados y fundidos
TIPOS Y USOS DE FUNDENTES
Clasificación según sus efectos operacionales.
Los fundentes también se clasifican según su efecto en los resultados finales de la operación de soldadura, existen dos categorías en este sentido y son los Activos y los Neutros:
Activos
Los fundentes activos son aquellos que causan un cambio sustancial en la composición química final del metal de soldadura cuando el voltaje de soldadura (y por consiguiente la cantidad de Fundente) es cambiado.
Los fundentes fundidos generalmente aportan grandes cantidades de Magnesio y Silicio al material de aporte, incrementando la resistencia, pero cuando se usa fundente activo para hacer soldaduras de multipases, puede ocurrir una excesiva acumulación de estos componentes resultando en una soldadura muy vulnerable a las grietas y las fracturas, los fundentes activos deben ser usados limitadamente en las soldaduras con pasos múltiples, especialmente sobre oxido y escamas metálicas, un cuidado especial en la regulación del voltaje es recomendado cuando se usa este tipo de fundentes en el procedimiento de soldadura con pasos múltiples para evitar la saturación de Magnesio y Silicio, en líneas generales, no es recomendado el uso de fundentes activos en soldaduras de pasos múltiples en laminas de un diámetro superior a los 25 Mm. (1").
Neutros
Como su clasificación misma lo dice este tipo de fundentes no causan cambios significativos en la composición química del metal de aporte, ni siquiera con variaciones de voltaje.
Los fundentes neutros no afectan la fuerza de la soldadura indiferentemente al voltaje o numero de pases de soldadura que se apliquen. Como regla general, los fundentes neutros deben ser parte de las especificaciones de las soldaduras con pases múltiples.
USO DE LOS FUNDENTES
El uso de estos es para fundir diferentes metales, entre ellos el plomo, el cobre, es muy utilizado en los sistemas de soldaduras, El éxito de la soldadura depende en gran parte del fundente.
El mismo evita la oxidación durante el proceso de soldadura, reduce los óxidos ya formadosy disminuye la tensión superficial del material de aporte.
Los fundentes aglomerados se hacen mezclando los constituyentes, finamente pulverizados, con una solución acuosa de un aglomerante tal como silicato sódico; la finalidad es producir partículas de unos pocos milímetros de diámetro formados por una masa de partículas más finas de los componentes minerales. Después de la aglomeración el fundente se seca a temperatura de hasta 800 oC.
Hay diferentes tipos de fundente cada uno para la diferente clase de soldadura
Fundente líquido para la soldadura blanda abase de cloruro de Zinc. l
Fundente en pasta para la soldadurablanda a base de cloruro de Zinc.
SAW = Submerged Arc Welding
Es un proceso de soldadura por arco eléctrico que usa un arco (o varios) entre el electrodo y el charco de soldadura. El arco y el metal fundido son protegidos por una capa de fundente granular sobre el área de soldadura. El proceso no requiere presión y el material de aporte es el alambre (o alambres) el cual es el que hace el arco o se puede alimentar por otra fuente supplementaria.
El fundente.
Entre las principales funciones del fundente para la soldadura de arco sumergido podríamos enumerar las siguientes:
Ø Protege la soldadura fundida de la interacción con la atmósfera.
Ø Limpia y desoxida la soldadura fundida.
Ø Ayuda a controlar las propiedades químicas y mecánicas del metal de aporte en la soldadura.
Ø Existen dos métodos importantes para elaborar los fundentes, Granulados y fundidos
TIPOS Y USOS DE FUNDENTES
Clasificación según sus efectos operacionales.
Los fundentes también se clasifican según su efecto en los resultados finales de la operación de soldadura, existen dos categorías en este sentido y son los Activos y los Neutros:
Activos
Los fundentes activos son aquellos que causan un cambio sustancial en la composición química final del metal de soldadura cuando el voltaje de soldadura (y por consiguiente la cantidad de Fundente) es cambiado.
Los fundentes fundidos generalmente aportan grandes cantidades de Magnesio y Silicio al material de aporte, incrementando la resistencia, pero cuando se usa fundente activo para hacer soldaduras de multipases, puede ocurrir una excesiva acumulación de estos componentes resultando en una soldadura muy vulnerable a las grietas y las fracturas, los fundentes activos deben ser usados limitadamente en las soldaduras con pasos múltiples, especialmente sobre oxido y escamas metálicas, un cuidado especial en la regulación del voltaje es recomendado cuando se usa este tipo de fundentes en el procedimiento de soldadura con pasos múltiples para evitar la saturación de Magnesio y Silicio, en líneas generales, no es recomendado el uso de fundentes activos en soldaduras de pasos múltiples en laminas de un diámetro superior a los 25 Mm. (1").
Neutros
Como su clasificación misma lo dice este tipo de fundentes no causan cambios significativos en la composición química del metal de aporte, ni siquiera con variaciones de voltaje.
Los fundentes neutros no afectan la fuerza de la soldadura indiferentemente al voltaje o numero de pases de soldadura que se apliquen. Como regla general, los fundentes neutros deben ser parte de las especificaciones de las soldaduras con pases múltiples.
USO DE LOS FUNDENTES
El uso de estos es para fundir diferentes metales, entre ellos el plomo, el cobre, es muy utilizado en los sistemas de soldaduras, El éxito de la soldadura depende en gran parte del fundente.
El mismo evita la oxidación durante el proceso de soldadura, reduce los óxidos ya formadosy disminuye la tensión superficial del material de aporte.
Los fundentes aglomerados se hacen mezclando los constituyentes, finamente pulverizados, con una solución acuosa de un aglomerante tal como silicato sódico; la finalidad es producir partículas de unos pocos milímetros de diámetro formados por una masa de partículas más finas de los componentes minerales. Después de la aglomeración el fundente se seca a temperatura de hasta 800 oC.
Hay diferentes tipos de fundente cada uno para la diferente clase de soldadura
Fundente líquido para la soldadura blanda abase de cloruro de Zinc. l
Fundente en pasta para la soldadurablanda a base de cloruro de Zinc.
Mig-Mag
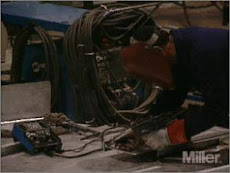
GMAW
Soldadura por arco metálico protegido con gas.
Proceso GMAW (Gas Metal Arc Welding)
MIG (Metal Inert Gas) MAG (Metal Active Gas)
La soldadura por arco con hilo electrodo fusible y protección gaseosa (procedimiento MIG y MAG) utiliza como material de aportación un hilo electrodo continúo y fisible, que se alimenta automáticamente, a través de la pistola de soldadura, a una velocidad regulable. El baño de fusión está completamente cubierto por un chorro de gas protector, que también se suministra a través de la pistola.
El procedimiento puede ser totalmente automático o semiautomático. Cuando la instalación es totalmente automática, la alimentación del alambre, la corriente de soldadura, el caudal de gas y la velocidad de desplazamiento a lo largo de la junta, se regulan previamente a los valores adecuados, y luego, todo funciona de forma automática.
En la soldadura semiautomática la alimentación del alambre, la corriente de soldadura y la circulación de gas, se regulan a los valores convenientes y funcionan automáticamente, pero la pistola hay que sostenerla y desplazarla manualmente. El soldador dirige la pistola a lo largo del cordón de soldadura, manteniendo la posición, longitud del arco y velocidad de avance adecuados.
Corriente de soldadura.
El tipo de corriente tiene una gran influencia sobre los resultados de la soldadura. La corriente continua con polaridad inversa, es la que permite obtener mejores resultados. En este caso, la mayor parte del claro se concentra sobre el baño de fusión, lo que mejora la penetración de la soldadura. Además, la corriente continúa con polaridad inversa, ejerce una enérgica acción de limpieza sobre el baño de fusión, lo que tiene gran importancia en la soldadura de metales que den óxidos pesados y difíciles de reducir, como en el caso del aluminio y el magnesio.
Modos de transferencia
1) Corto circuito
2) Globular
3) Spray
4) Spray pulsado
Clasificación de los Electrodos
ER Electrodo continuo (E), ó varilla (R).
XXX Resistencia mínima a la tensión, en miles de psi (lb/in2)
S Metal de aporte es sólido (S) ó Compuesto (C).
X Composición química del electrodo sólido ó la composición química del depósito producido por un electrodo compuesto.
Gases de protección
Sus funciones principales son:
¨ Formar una campana de protección para el metal líquido contra la atmósfera.
¨ Estabilizar el arco.
¨ Afecta la forma de la columna de plasma y permite los diferentes modos de transferencia.
Los gases puros que con mayor frecuencia se utilizan como gas de protección (ó una mezcla de ellos) son:
¨ Argón (Ar)
¨ Bióxido de carbono (CO2)
¨ Oxígeno (O2)
¨ Helio (He)
¨ Hidrógeno (H2)
¨ Nitrógeno (N2)
Proceso GMAW (Gas Metal Arc Welding)
MIG (Metal Inert Gas) MAG (Metal Active Gas)
La soldadura por arco con hilo electrodo fusible y protección gaseosa (procedimiento MIG y MAG) utiliza como material de aportación un hilo electrodo continúo y fisible, que se alimenta automáticamente, a través de la pistola de soldadura, a una velocidad regulable. El baño de fusión está completamente cubierto por un chorro de gas protector, que también se suministra a través de la pistola.
El procedimiento puede ser totalmente automático o semiautomático. Cuando la instalación es totalmente automática, la alimentación del alambre, la corriente de soldadura, el caudal de gas y la velocidad de desplazamiento a lo largo de la junta, se regulan previamente a los valores adecuados, y luego, todo funciona de forma automática.
En la soldadura semiautomática la alimentación del alambre, la corriente de soldadura y la circulación de gas, se regulan a los valores convenientes y funcionan automáticamente, pero la pistola hay que sostenerla y desplazarla manualmente. El soldador dirige la pistola a lo largo del cordón de soldadura, manteniendo la posición, longitud del arco y velocidad de avance adecuados.
Corriente de soldadura.
El tipo de corriente tiene una gran influencia sobre los resultados de la soldadura. La corriente continua con polaridad inversa, es la que permite obtener mejores resultados. En este caso, la mayor parte del claro se concentra sobre el baño de fusión, lo que mejora la penetración de la soldadura. Además, la corriente continúa con polaridad inversa, ejerce una enérgica acción de limpieza sobre el baño de fusión, lo que tiene gran importancia en la soldadura de metales que den óxidos pesados y difíciles de reducir, como en el caso del aluminio y el magnesio.
Modos de transferencia
1) Corto circuito
2) Globular
3) Spray
4) Spray pulsado
Clasificación de los Electrodos
ER Electrodo continuo (E), ó varilla (R).
XXX Resistencia mínima a la tensión, en miles de psi (lb/in2)
S Metal de aporte es sólido (S) ó Compuesto (C).
X Composición química del electrodo sólido ó la composición química del depósito producido por un electrodo compuesto.
Gases de protección
Sus funciones principales son:
¨ Formar una campana de protección para el metal líquido contra la atmósfera.
¨ Estabilizar el arco.
¨ Afecta la forma de la columna de plasma y permite los diferentes modos de transferencia.
Los gases puros que con mayor frecuencia se utilizan como gas de protección (ó una mezcla de ellos) son:
¨ Argón (Ar)
¨ Bióxido de carbono (CO2)
¨ Oxígeno (O2)
¨ Helio (He)
¨ Hidrógeno (H2)
¨ Nitrógeno (N2)
Tig
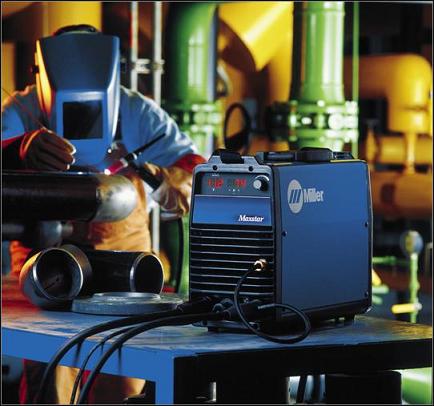
Pistola Tig
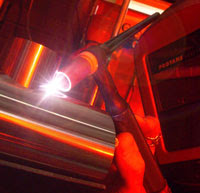
GTAW
Proceso GTAW (TIG)
Gas Tungsten Arc Welding Tungsten Inert Gas
En la operación de ensamblaje de las piezas de carrocería, es imprescindible usar métodos y equipos de soldaduras que nos aseguren una buena calidad en las uniones, que se alteren lo menos posible las propiedades mecánicas de la chapa y que no generen focos de corrosión. De ello dependerá tanto la calidad de determinación, como la seguridad del vehículo reparado. Uno de los métodos que más nos garantiza estos resultados, es el sistema de soldadura MIG -MAG, que nos proporciona una unión que presenta excelentes características de resistencia mecánica.
Historia de la soldadura TIG, MIG
En el año de 1900 se otorgó una patente relacionada con electrodos rodeado por un gas inerte. Los experimentos con este tipo de soldadura continuaron durante las décadas de 1920 y 1930, sin embargo hasta 1940 se dio gran atención al proceso GTAW. Hasta antes de comenzar la segunda guerra mundial se habían hecho pocos experimentos por que los gases inertes eran muy costosos, pero durante la guerra, la industria de la aviación necesita con urgencia un método más rápido y fácil para soldar aluminio y magnesio para acelerar la producción.
Debido a los beneficios logrados en la producción, se justificó el costo adicional del empleo del gas inerte en gran escala. Aunque la producción de este gas es mucho más rápida y económica, todavía representa un gasto adicional pero justificable.
En la década de 1940 se otorgó una patente de un proceso para eliminar un electrodo de alambre en forma continua a través de un arco protegido con gas, Este fue un principio del proceso MIG (metal y gas inerte), que ahora tiene la denominación oficial de AWS y de CSA como soldadura con gas y arco de metal (GMAW). Este tipo de soldadura con arco se ha perfeccionado y agilizado desde sus primeros días, además se han creado procesos relacionados. En alguno de ellos se emplea un electrodo, de alambre desnudo, protegido con gas inerte, en otro se emplea un electrodo recubierto con fundente similar a los convencionales para soldadura con arco. En algunos otros se utiliza también un electrodo hueco o tubular que tiene núcleo o fundente. En determinados procesos se hace uso de una combinación de electrodo con núcleo fundente y un gas de protector.
También para transferir el metal fundido a través del arco, se utilizan diferentes métodos que pueden ser manuales semiautomáticos ó automáticos. La GMAW es ahora uno de los procesos más importantes en la industria de la soldadura.
El objetivo fundamental en cualquier operación de soldadura es el de conseguir una junta con la misma característica del metal base. Este resultado solo puede obtenerse si el baño de fusión está completamente aislado de la atmósfera durante toda la operación de soldeo. De no cumplirse esta condición, tanto el oxígeno como el nitrógeno del aire serán absorbidos por el metal en estado de fusión la soldadura quedará porosa y frágil. En la soldadura por arco con protección gaseosa, se utiliza como medio de protección un chorro de gas que rodea el arco y el baño de fusión, impidiendo la contaminación de la soldadura.
Ventajas específicas de la soldadura por arco con protección gaseosa TIG.
Puesto que al gas protector impide el contacto entre la atmósfera y el baño de fusión, los iones obtenidos son más resistentes, más dúctiles y menos sensibles a la corrosión, que las que se obtienen por la mayor parte de los procedimientos.
La protección gaseosa simplifica notablemente el soldeo de metales no ferrosos, por no requerir el empleo de desoxidantes. Los procedimientos que exigen la aplicación de los residuos de los mimos una vez realizada la soldadura. Además, con el empleo de estos desoxidantes, siempre hay el peligro de deformación de soldaduras e inclusiones de escoria.
Otra ventaja de la soldadura por arco con protección gaseosa es la que permite obtener soldaduras limpias, sanas y uniformes, debido a la escasez de humos y proyecciones, por otra parte, dado que la rotación gaseosa que rodea al arco transparente, el soldador puede ver claramente lo que está haciendo en todo momento, lo que repercute favorablemente en la calidad de la soldadura.
La soldadura puede realizarse en todas las posiciones con un mínimo de proyecciones, esto que la superficie del cordón presenta una graneza, pude suprimirse, o reducirse sensiblemente, u operaciones de acabado, lo que incide favorablemente en los costos de producción. Ultimo, también es menor la deformación de las inmediaciones del cordón de soldadura.
Variantes de los procedimientos.
Cada uno de estos procedimientos presenta sus ventajas y características, pero ambos coinciden en producir soldadura bien penetradas y relativamente libres de contaminación atmosférica.
La mayor parte de los metales industriales pueden soldarse fácilmente uno u otro procedimiento. Esto incluye a metales como el aluminio, magnesio, acero débilmente aliados, aceros al carbón, aceros inoxidables, cobre, níquel, monel, inconel, titanio y otros.
Ambos procedimientos pueden aplicarse manualmente o automáticamente. En la soldadura semiautomática, el soldador controla la dirección y la velocidad de avance. En el soldeo automático, la inclinación de cordón, el espesor de la aportación, la velocidad de avance. En el soldeo automático, la inclinación del cordón, el espesor de la aportación, la velocidad de avance, la dirección, etc. Están controlados por el equipo.
Metales de aportación para la soldadura con protección gaseosa.
Normalmente la soldadura TIG de espesores finos pueden realizarse sin material de aportación, sin embargo al aumentar el espesor, es necesario aportar material para rellenar la junta. En algunos casos cuando se quiere reforzar la junta. También se aporta material en la soldadura de espesores finos.
El metal de aportación debe ser de la misma composición que el metal base. Así para el soldeo de aceros al carbón, se utilizan varillas de acero al carbón; para el soldeo de aluminio, varillas de aluminio; y así sucesivamente en algunos, casos, puede utilizarse satisfactoriamente como material de aportación una tira obtenida de las propias chapas a soldar.
Como aportación para la soldadura TIG deben utilizarse varillas fabricadas expresamente para este procedimiento. Estas varillas se clasifican igual que los alambres utilizados en MIG. Las varillas de acero ordinario, cobreadas que se utilizan en la soldadura oxiacetilénica, no deben aplicarse a la soldadura TIG porque tienden a contaminar el electrodo de Tungsteno. Con vistas a conseguir soldaduras sanas y para reducir las proyecciones, las varillas de aportación para el procedimiento TIG llevan mayores cantidades de sustancias desoxidantes.
En general, el diámetro de la varilla debe ser aproximadamente igual al espesor de las piezas a soldar.
Seguridad Industrial
Las investigaciones de las compañías de seguridad y organizaciones de seguridad han demostrado que la soldadura no es más peligrosa que cualquier otra ocupación o trabajo artesanal. Sin embargo, igual que en cualquiera de ellos existen ciertas precauciones que se deben tomar para la protección de uno mismo y de los demás.
Seguridad personal.
Ø Use siempre gafas protectoras cuando trabaje con un soplete encendido.
Ø Utilice guantes de un material resistente al calor como el cuero curtido al cromo, para protegerse las manos.
Ø No deben utilizarse zapatos abiertos ni deportivos. Hay que emplear calzado de seguridad con puntas de acero.
Ø Mantenga la ropa libre de aceite o grasa.
Ø No permite que la ropa se sature con oxígeno.
Ø Utilice ropa resistente al fuego (delantal, manguitos, perneras, guantes).
Ø Use las mangas, las bolsas sueltas cerradas y las valencianas del pantalón desdobladas.
Ø Utilice cascos o caretas con el vidrio de filtro del grado correcto. Cuando se use careta de mano en lugar del casco, hay que aplicar las mismas precauciones.
Ø Compruebe siempre que los vidrios no estén rotos ni agrietados antes de empezar a soldar.
Ø Utilice gafas protectoras cuando elimine con un cincel la escoria de la soldadura.
Ø No lleve en el bolsillo fósforos ni encendedores de gas o de líquido.
Ø No trabaje con equipo que sospeche que está defectuoso, informe de inmediato a su instructor.
Ø Nunca efectúe soldadura con arco en lugar que esté húmedo o mojado.
Ø Cerciórese que las demás personas estén protegidas contra los rayos e la luz antes de empezar a soldar.
Ø Para probar si hay radiación de calor, ponga la palma de su mano encima de la pieza del metal, pero sin tocarla. No toque la pieza con la mano desnuda aunque no produzca brillo por el calor.
Prevención de incendios.
Los incendios pueden ocurrir en donde se efectúa cualquier operación de soldadura o corte si se permite que cualquier material combustible haga contacto con el arco, la flama, las chispas o la escoria caliente. Para prevenir incendios:
Ø Antes de empezar a trabajar retire todo el material combustible donde vaya soldar o cortar.
Ø Si no se pueden retirar los materiales combustibles, ponga barreras contra fuego, como lámparas o láminas metálicas o manteas resistentes al fuego.
Ø Conozca de antemano el lugar exacto en donde están los extinguidores de incendio.
Ø La soldadura o el corte no se deben efectuar en lugares en donde hay polvos o gases, o en zonas donde se pintan con pistola de aires pues pueden ocurrir explosiones o incendios.
Ø Nunca solde ni corte barriles, tambores, tanques o recipientes hasta que estén absolutamente limpios.
Ventilación y gases de protección.
Como en la soldadura y el corte se producen humo, polvo y vapores, todas las operaciones se deben efectuar en lugares bien ventilados. Se han realizado y continúan haciéndose muchos estudios acerca de todos los tipos de vapores, gases y otras sustancias que producen, durante le proceso de soldadura, las varillas y electrodos y el metal que se va a soldar. También están en estudio los vapores que se desprenden durante el proceso y que se podrían convertir en compuestos tóxicos por la radiación ultravioleta en el arco en sí.
Antes de empezar a soldar o a cortar, compruebe que la ventilación es adecuada para pulsar el humo, polvo y vapores que podrían ser dañinos para la salud.
Lea y siga las instrucciones que aparecen en las etiquetas de los fundentes y de los metales de aporte.
Determine el metal con el que vaya a trabajar y tome las precauciones necesarias con respecto a los vapores y a la ventilación adecuada.
Se requiere un respirador con suministro de aire, además de la ventilación normal cuando se utilizan metales como el plomo, latón, bronce galvanizado, cadmio.
No utilice una máquina de soldadura impulsada por un motor de combustión interna en un lugar cerrado, salvo que se puedan expulsar los gases del escape fuera de ése lugar.
El gas protector para soldadura TIG; puede ser argón, el helio o una mezcla de ambos gases. El más utilizado es el primero, debido a que es más barato que el helio.
El argón es 1.4 más pesado que el aire y unas 10 veces más pesado que el helio. La viscosidad de ambos gases es muy parecida. Puesto que el argón es más pesado que el aire, procura una mejor protección de la soldadura. Además, con el argón, la atmósfera que rodea el arco es más clara, lo que permite un mejor control del baño de fusión del propio arco.
Normalmente, el argón produce una acción de limpieza del baño de fusión más enérgica que otros gases, especialmente en la soldadura de aluminio y magnesio con corriente alterna.
Otra ventaja de este gas la encontramos en el arco, que es suave y de gran estabilidad. Por otra parte, puede que en atmósfera de argón la tensión de arco es más baja, hay menos peligro de perforar la piezas cuando se soldan en espesores finos. Consecuentemente, el argón suele utilizarse para la soldadura manual, o con máquinas automáticas de pequeña velocidad de soldeo, en espesores iguales o inferiores a 3 mm.
El argón también permite un mejor control de baño de fusión cuando se solda en vertical o en techo.
Además como regla general, el arco es más fácil de cebar en argón que en helio, y para una velocidad de soldeo dada, el cordón obtenido es más estrecho y la zona afectada por el calor es más reducida.
Cuando la velocidad de soldeo es el factor determinante, especialmente en soldadura automática, o en el soldeo de espesores o de metales e levada conductividad térmica, en algunos casos se recurre al helio como gas de protección. El helio permite obtener mayores velocidades de soldeo debido a que para una intensidad dada, la tensión de arco es mayor. Puesto que la tensión del arco en atmósfera de helio es mayor que en el caso del argón, con una intensidad de corriente más baja, puede conseguirse la misma potencia de arco, y de esta forma trabajarse a elevadas velocidades de soldeo sin necesidad de utilizar grandes intensidades de corriente.
Cuando quiere mejorar la aportación de calor sin perder las ventajas típicas del argón, se recurre a las mezclas argón - helio.
El argón y el helio se suministran en botellas de acero que contienen unos 10 m3 de gas a una presión de 150 kg./cm2 .
Para reducir la presión y control el caudal del gas se utilizan manorreductores caudalímetro. Estos aparatos suelen venir calibrados en litros por minuto.
El caudal de gas, que depende del espesor y naturaleza del metal a soldar, puede regularse mediante un mando situado en el caudalímetro.
Equipo de protección.
Para protegerse de las radiaciones del arco hay que utilizar una pantalla de cabeza, similar a las que se emplean en la soldadura con electrodos revestidos. La tonalidad el cristal depende de la intensidad de la corriente. Además deben llevarse las ropas de protección adecuadas, tales como mandil y guantes.
Gas Tungsten Arc Welding Tungsten Inert Gas
En la operación de ensamblaje de las piezas de carrocería, es imprescindible usar métodos y equipos de soldaduras que nos aseguren una buena calidad en las uniones, que se alteren lo menos posible las propiedades mecánicas de la chapa y que no generen focos de corrosión. De ello dependerá tanto la calidad de determinación, como la seguridad del vehículo reparado. Uno de los métodos que más nos garantiza estos resultados, es el sistema de soldadura MIG -MAG, que nos proporciona una unión que presenta excelentes características de resistencia mecánica.
Historia de la soldadura TIG, MIG
En el año de 1900 se otorgó una patente relacionada con electrodos rodeado por un gas inerte. Los experimentos con este tipo de soldadura continuaron durante las décadas de 1920 y 1930, sin embargo hasta 1940 se dio gran atención al proceso GTAW. Hasta antes de comenzar la segunda guerra mundial se habían hecho pocos experimentos por que los gases inertes eran muy costosos, pero durante la guerra, la industria de la aviación necesita con urgencia un método más rápido y fácil para soldar aluminio y magnesio para acelerar la producción.
Debido a los beneficios logrados en la producción, se justificó el costo adicional del empleo del gas inerte en gran escala. Aunque la producción de este gas es mucho más rápida y económica, todavía representa un gasto adicional pero justificable.
En la década de 1940 se otorgó una patente de un proceso para eliminar un electrodo de alambre en forma continua a través de un arco protegido con gas, Este fue un principio del proceso MIG (metal y gas inerte), que ahora tiene la denominación oficial de AWS y de CSA como soldadura con gas y arco de metal (GMAW). Este tipo de soldadura con arco se ha perfeccionado y agilizado desde sus primeros días, además se han creado procesos relacionados. En alguno de ellos se emplea un electrodo, de alambre desnudo, protegido con gas inerte, en otro se emplea un electrodo recubierto con fundente similar a los convencionales para soldadura con arco. En algunos otros se utiliza también un electrodo hueco o tubular que tiene núcleo o fundente. En determinados procesos se hace uso de una combinación de electrodo con núcleo fundente y un gas de protector.
También para transferir el metal fundido a través del arco, se utilizan diferentes métodos que pueden ser manuales semiautomáticos ó automáticos. La GMAW es ahora uno de los procesos más importantes en la industria de la soldadura.
El objetivo fundamental en cualquier operación de soldadura es el de conseguir una junta con la misma característica del metal base. Este resultado solo puede obtenerse si el baño de fusión está completamente aislado de la atmósfera durante toda la operación de soldeo. De no cumplirse esta condición, tanto el oxígeno como el nitrógeno del aire serán absorbidos por el metal en estado de fusión la soldadura quedará porosa y frágil. En la soldadura por arco con protección gaseosa, se utiliza como medio de protección un chorro de gas que rodea el arco y el baño de fusión, impidiendo la contaminación de la soldadura.
Ventajas específicas de la soldadura por arco con protección gaseosa TIG.
Puesto que al gas protector impide el contacto entre la atmósfera y el baño de fusión, los iones obtenidos son más resistentes, más dúctiles y menos sensibles a la corrosión, que las que se obtienen por la mayor parte de los procedimientos.
La protección gaseosa simplifica notablemente el soldeo de metales no ferrosos, por no requerir el empleo de desoxidantes. Los procedimientos que exigen la aplicación de los residuos de los mimos una vez realizada la soldadura. Además, con el empleo de estos desoxidantes, siempre hay el peligro de deformación de soldaduras e inclusiones de escoria.
Otra ventaja de la soldadura por arco con protección gaseosa es la que permite obtener soldaduras limpias, sanas y uniformes, debido a la escasez de humos y proyecciones, por otra parte, dado que la rotación gaseosa que rodea al arco transparente, el soldador puede ver claramente lo que está haciendo en todo momento, lo que repercute favorablemente en la calidad de la soldadura.
La soldadura puede realizarse en todas las posiciones con un mínimo de proyecciones, esto que la superficie del cordón presenta una graneza, pude suprimirse, o reducirse sensiblemente, u operaciones de acabado, lo que incide favorablemente en los costos de producción. Ultimo, también es menor la deformación de las inmediaciones del cordón de soldadura.
Variantes de los procedimientos.
Cada uno de estos procedimientos presenta sus ventajas y características, pero ambos coinciden en producir soldadura bien penetradas y relativamente libres de contaminación atmosférica.
La mayor parte de los metales industriales pueden soldarse fácilmente uno u otro procedimiento. Esto incluye a metales como el aluminio, magnesio, acero débilmente aliados, aceros al carbón, aceros inoxidables, cobre, níquel, monel, inconel, titanio y otros.
Ambos procedimientos pueden aplicarse manualmente o automáticamente. En la soldadura semiautomática, el soldador controla la dirección y la velocidad de avance. En el soldeo automático, la inclinación de cordón, el espesor de la aportación, la velocidad de avance. En el soldeo automático, la inclinación del cordón, el espesor de la aportación, la velocidad de avance, la dirección, etc. Están controlados por el equipo.
Metales de aportación para la soldadura con protección gaseosa.
Normalmente la soldadura TIG de espesores finos pueden realizarse sin material de aportación, sin embargo al aumentar el espesor, es necesario aportar material para rellenar la junta. En algunos casos cuando se quiere reforzar la junta. También se aporta material en la soldadura de espesores finos.
El metal de aportación debe ser de la misma composición que el metal base. Así para el soldeo de aceros al carbón, se utilizan varillas de acero al carbón; para el soldeo de aluminio, varillas de aluminio; y así sucesivamente en algunos, casos, puede utilizarse satisfactoriamente como material de aportación una tira obtenida de las propias chapas a soldar.
Como aportación para la soldadura TIG deben utilizarse varillas fabricadas expresamente para este procedimiento. Estas varillas se clasifican igual que los alambres utilizados en MIG. Las varillas de acero ordinario, cobreadas que se utilizan en la soldadura oxiacetilénica, no deben aplicarse a la soldadura TIG porque tienden a contaminar el electrodo de Tungsteno. Con vistas a conseguir soldaduras sanas y para reducir las proyecciones, las varillas de aportación para el procedimiento TIG llevan mayores cantidades de sustancias desoxidantes.
En general, el diámetro de la varilla debe ser aproximadamente igual al espesor de las piezas a soldar.
Seguridad Industrial
Las investigaciones de las compañías de seguridad y organizaciones de seguridad han demostrado que la soldadura no es más peligrosa que cualquier otra ocupación o trabajo artesanal. Sin embargo, igual que en cualquiera de ellos existen ciertas precauciones que se deben tomar para la protección de uno mismo y de los demás.
Seguridad personal.
Ø Use siempre gafas protectoras cuando trabaje con un soplete encendido.
Ø Utilice guantes de un material resistente al calor como el cuero curtido al cromo, para protegerse las manos.
Ø No deben utilizarse zapatos abiertos ni deportivos. Hay que emplear calzado de seguridad con puntas de acero.
Ø Mantenga la ropa libre de aceite o grasa.
Ø No permite que la ropa se sature con oxígeno.
Ø Utilice ropa resistente al fuego (delantal, manguitos, perneras, guantes).
Ø Use las mangas, las bolsas sueltas cerradas y las valencianas del pantalón desdobladas.
Ø Utilice cascos o caretas con el vidrio de filtro del grado correcto. Cuando se use careta de mano en lugar del casco, hay que aplicar las mismas precauciones.
Ø Compruebe siempre que los vidrios no estén rotos ni agrietados antes de empezar a soldar.
Ø Utilice gafas protectoras cuando elimine con un cincel la escoria de la soldadura.
Ø No lleve en el bolsillo fósforos ni encendedores de gas o de líquido.
Ø No trabaje con equipo que sospeche que está defectuoso, informe de inmediato a su instructor.
Ø Nunca efectúe soldadura con arco en lugar que esté húmedo o mojado.
Ø Cerciórese que las demás personas estén protegidas contra los rayos e la luz antes de empezar a soldar.
Ø Para probar si hay radiación de calor, ponga la palma de su mano encima de la pieza del metal, pero sin tocarla. No toque la pieza con la mano desnuda aunque no produzca brillo por el calor.
Prevención de incendios.
Los incendios pueden ocurrir en donde se efectúa cualquier operación de soldadura o corte si se permite que cualquier material combustible haga contacto con el arco, la flama, las chispas o la escoria caliente. Para prevenir incendios:
Ø Antes de empezar a trabajar retire todo el material combustible donde vaya soldar o cortar.
Ø Si no se pueden retirar los materiales combustibles, ponga barreras contra fuego, como lámparas o láminas metálicas o manteas resistentes al fuego.
Ø Conozca de antemano el lugar exacto en donde están los extinguidores de incendio.
Ø La soldadura o el corte no se deben efectuar en lugares en donde hay polvos o gases, o en zonas donde se pintan con pistola de aires pues pueden ocurrir explosiones o incendios.
Ø Nunca solde ni corte barriles, tambores, tanques o recipientes hasta que estén absolutamente limpios.
Ventilación y gases de protección.
Como en la soldadura y el corte se producen humo, polvo y vapores, todas las operaciones se deben efectuar en lugares bien ventilados. Se han realizado y continúan haciéndose muchos estudios acerca de todos los tipos de vapores, gases y otras sustancias que producen, durante le proceso de soldadura, las varillas y electrodos y el metal que se va a soldar. También están en estudio los vapores que se desprenden durante el proceso y que se podrían convertir en compuestos tóxicos por la radiación ultravioleta en el arco en sí.
Antes de empezar a soldar o a cortar, compruebe que la ventilación es adecuada para pulsar el humo, polvo y vapores que podrían ser dañinos para la salud.
Lea y siga las instrucciones que aparecen en las etiquetas de los fundentes y de los metales de aporte.
Determine el metal con el que vaya a trabajar y tome las precauciones necesarias con respecto a los vapores y a la ventilación adecuada.
Se requiere un respirador con suministro de aire, además de la ventilación normal cuando se utilizan metales como el plomo, latón, bronce galvanizado, cadmio.
No utilice una máquina de soldadura impulsada por un motor de combustión interna en un lugar cerrado, salvo que se puedan expulsar los gases del escape fuera de ése lugar.
El gas protector para soldadura TIG; puede ser argón, el helio o una mezcla de ambos gases. El más utilizado es el primero, debido a que es más barato que el helio.
El argón es 1.4 más pesado que el aire y unas 10 veces más pesado que el helio. La viscosidad de ambos gases es muy parecida. Puesto que el argón es más pesado que el aire, procura una mejor protección de la soldadura. Además, con el argón, la atmósfera que rodea el arco es más clara, lo que permite un mejor control del baño de fusión del propio arco.
Normalmente, el argón produce una acción de limpieza del baño de fusión más enérgica que otros gases, especialmente en la soldadura de aluminio y magnesio con corriente alterna.
Otra ventaja de este gas la encontramos en el arco, que es suave y de gran estabilidad. Por otra parte, puede que en atmósfera de argón la tensión de arco es más baja, hay menos peligro de perforar la piezas cuando se soldan en espesores finos. Consecuentemente, el argón suele utilizarse para la soldadura manual, o con máquinas automáticas de pequeña velocidad de soldeo, en espesores iguales o inferiores a 3 mm.
El argón también permite un mejor control de baño de fusión cuando se solda en vertical o en techo.
Además como regla general, el arco es más fácil de cebar en argón que en helio, y para una velocidad de soldeo dada, el cordón obtenido es más estrecho y la zona afectada por el calor es más reducida.
Cuando la velocidad de soldeo es el factor determinante, especialmente en soldadura automática, o en el soldeo de espesores o de metales e levada conductividad térmica, en algunos casos se recurre al helio como gas de protección. El helio permite obtener mayores velocidades de soldeo debido a que para una intensidad dada, la tensión de arco es mayor. Puesto que la tensión del arco en atmósfera de helio es mayor que en el caso del argón, con una intensidad de corriente más baja, puede conseguirse la misma potencia de arco, y de esta forma trabajarse a elevadas velocidades de soldeo sin necesidad de utilizar grandes intensidades de corriente.
Cuando quiere mejorar la aportación de calor sin perder las ventajas típicas del argón, se recurre a las mezclas argón - helio.
El argón y el helio se suministran en botellas de acero que contienen unos 10 m3 de gas a una presión de 150 kg./cm2 .
Para reducir la presión y control el caudal del gas se utilizan manorreductores caudalímetro. Estos aparatos suelen venir calibrados en litros por minuto.
El caudal de gas, que depende del espesor y naturaleza del metal a soldar, puede regularse mediante un mando situado en el caudalímetro.
Equipo de protección.
Para protegerse de las radiaciones del arco hay que utilizar una pantalla de cabeza, similar a las que se emplean en la soldadura con electrodos revestidos. La tonalidad el cristal depende de la intensidad de la corriente. Además deben llevarse las ropas de protección adecuadas, tales como mandil y guantes.
Electrodo Revestido
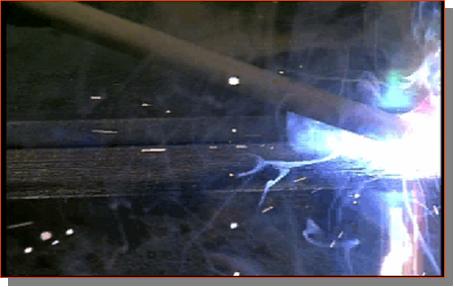
SMAW
Soldadura por Electrodo Manual Revestido.
Proceso SMAW (Stick Metal Arc Welding).
El calor necesario para la lograr la fusión de los componentes se obtiene de un arco eléctrico formado entre un electrodo recubierto, en forma de varilla, y la pieza de trabajo.
Fuentes de poder
Los tipos más comunes son:
Ø Transformadores
Ø Transformadores-rectificadores
Ø Motosoldadoras (diesel ó gasolina)
Ø Inversores
Funciones del recubrimiento del electrodo:
Ø Proporcionar un gas para crear una atmósfera inerte y que el metal líquido que está siendo transferido al depósito se contamine.
Ø Establecer las características eléctricas del electrodo.
Sistema de Clasificación de los Electrodos
Las especificaciones AWS A5.1, la cual se refiere a los electrodos para soldaduras de aceros al carbón, trabaja con la siguiente designación:
E-XXXX
De donde:
E Electrodo.
XX Son los dos primeros dígitos que nos muestran la mínima resistencia a la tracción.
X El tercer dígito nos muestra la posición de trabajo del electrodo.
X El cuarto dígito el tipo de recubrimiento y corriente recomendada.
Selección y Recomendaciones para La Aplicación de los Electrodos.
Existen 7 factores fundamentales en la selección de electrodos para la soldadura por arco eléctrico:
1. Identificar el metal base.
2. Conocer el tipo de corriente disponible para la soldadura, o sea, si se cuenta con Corriente continúa o alterna.
3. Conocer la posición con la cual debe efectuarse la soldadura.
4. Conocer espesor y forma del metal base.
5. Conocer el diseño de la junta.
6. Conocer las especificaciones de servicios requeridas para la junta.
7. Tener eficiencia y rapidez en la operación.
Proceso SMAW (Stick Metal Arc Welding).
El calor necesario para la lograr la fusión de los componentes se obtiene de un arco eléctrico formado entre un electrodo recubierto, en forma de varilla, y la pieza de trabajo.
Fuentes de poder
Los tipos más comunes son:
Ø Transformadores
Ø Transformadores-rectificadores
Ø Motosoldadoras (diesel ó gasolina)
Ø Inversores
Funciones del recubrimiento del electrodo:
Ø Proporcionar un gas para crear una atmósfera inerte y que el metal líquido que está siendo transferido al depósito se contamine.
Ø Establecer las características eléctricas del electrodo.
Sistema de Clasificación de los Electrodos
Las especificaciones AWS A5.1, la cual se refiere a los electrodos para soldaduras de aceros al carbón, trabaja con la siguiente designación:
E-XXXX
De donde:
E Electrodo.
XX Son los dos primeros dígitos que nos muestran la mínima resistencia a la tracción.
X El tercer dígito nos muestra la posición de trabajo del electrodo.
X El cuarto dígito el tipo de recubrimiento y corriente recomendada.
Selección y Recomendaciones para La Aplicación de los Electrodos.
Existen 7 factores fundamentales en la selección de electrodos para la soldadura por arco eléctrico:
1. Identificar el metal base.
2. Conocer el tipo de corriente disponible para la soldadura, o sea, si se cuenta con Corriente continúa o alterna.
3. Conocer la posición con la cual debe efectuarse la soldadura.
4. Conocer espesor y forma del metal base.
5. Conocer el diseño de la junta.
6. Conocer las especificaciones de servicios requeridas para la junta.
7. Tener eficiencia y rapidez en la operación.
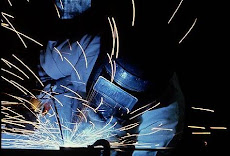
Los electrodos se clasifican por su revestimiento en cinco tipos:
Tipo Celulósico.- Este electrodo contiene en su revestimiento 45% de celulosa. El arco eléctrico del electrodo calienta el recubrimiento descomponiendo la celulosa en CO, C02 y vapor de agua. Poseen otros elementos como bióxido de titanio que es formador de escoria, ferro manganeso como desoxidante o reductor. Asbesto como formador de arco y escoria, Silicato de potasio como liga de compuestos y purificador, silicato de sodio como liga de compuestos.
Este tipo de electrodo forma poca escoria siendo principalmente usado en soldadura vertical descendente y altas penetraciones, efecto causado por la capa gaseosa del recubrimiento, el electrodo presenta un cordón poco vistoso por su tipo irregular y alto chisporroteo.
Su uso se debe a cordones donde es necesario obtener doble acabado (piezas que no pueden soldar por ambos lados) por ejemplo en tuberías en el cordón de fondeo y posiciones difíciles.
Son excelentes para soldar aceros con más del 0,25% de carbono y aceros efervescentes.
Base de Rutilo.- Se destacan por su tipo de acabado y facilidad de manejo su escoria se remueve fácilmente y en algunos casos sola. Su contenido de hidrógeno es alto y no requiere un proceso de exactitud.
El nombre del electrodo es propiamente incorrecto ya que el contenido de rutilo es principalmente un bióxido de titanio. Por este tipo de revestimiento se presta el electrodo para corregir fallas en el tipo de preparación.
Este electrodo se utiliza en trabajos de serie y de pocos requerimientos.
Bajo Hidrógeno.- Este tipo de electrodo produce las soldaduras de más alta calidad debido a su bajo contenido de carbono e hidrogeno. Como elementos componentes del revestimiento tiene:
Carbonato de Calcio.- Da una reacción básica a ¡a escoria, absorbe y neutraliza impurezas del azufre. Fluorita.- Neutraliza las impurezas del fósforo de tipo ácido que son perjudiciales. Manganeso.- Liga el azufre evitando los sulfuros y proporciona elasticidad a los depósitos.
Se utiliza este tipo de electrodos en aceros con alto contenido de carbono 0.25% aceros efervescentes y en construcción rígida.
Oxido de Fierro.- Este electrodo se caracteriza por su tipo de escoria liquida (propicia para soldar en vertical descendente) y su alta velocidad de deposito y limpieza.
Posee un alto contenido de manganeso como agente reductor y liga impurezas con la asistencia de silicatos formadores de escoria.
Polvo de Fierro.- Este electrodo contiene un 50% de fierro en el revestimiento, logrando hacer depósitos de 2.5 veces el alma del electrodo. Este electrodo. Fue hecho para competir con los procesos semiautomáticos en la industria, el tipo de electrodos más usados son el 7018, 7024, el primero en bajo hidrógeno y el segundo un parecido al 7014.
CLASIFICACIÓN DE LOS ELECTRODOS DE ACERO AL CARBÓN SEGÚN LA DESIGNACIÓN ISO
El sistema ISO de designación de los elementos de acero de bajo carbono es aproximadamente similar, o sea, nos proporciona las mismas informaciones del AWS, pero de la siguiente manera:
Ejemplo: ISO: E-51 4, B-120 26 H (corresponde a la clase. AWS E-7018)
E (Ref. "a") = La letra "E" encabeza al igual que la clasificación AWS. la designación del electrodo, y nos indica que el material de aporte es, electrodo ( véase el cuadro Características mecánicas.)
51 (Ref. "b") = quiere decir que pertenece al grupo "4" de los electrodos "51", con limite a la rotura de 510 - 610 N/Mm2 (véase cuadro características mecánicas).
4 (Ref. "c") =indica que pertenece al grupo "4" de los electrodos "51", con límite a la rotura de 510 - 610 N/mm2 , con un alargamiento mínimo de 20%, y una resistencia al impacto KV. min. de 352 , a una temperatura de ?300c. (Véase cuadro Características mecánicas).
B (Ref. "d") = se refiere a que este electrodo es del tipo con revestimiento básico (bajo hidrógeno) (véase cuadro Características mecánicas),
120 = se refiere al rendimiento del electrodo en %, en esté caso e¡ revestimiento produce aproximadamente un 120% . La designación del porcentaje del rendimiento se aplica para los electrodos con rendimiento se aplica para los electrodos con rendimiento del 110% en adelante.
26 (Ref. "E" y "F") = estos números nos proporcionan las características de aplicación referente a la posición de soldadura, tipo de corriente y polaridad, en la siguiente forma:
2 (Ref. "e") = se refiere a las posiciones de soldadura, en este caso el "2" nos indica que es apto para s posiciones excepto la posición e,
Este tipo de electrodo forma poca escoria siendo principalmente usado en soldadura vertical descendente y altas penetraciones, efecto causado por la capa gaseosa del recubrimiento, el electrodo presenta un cordón poco vistoso por su tipo irregular y alto chisporroteo.
Su uso se debe a cordones donde es necesario obtener doble acabado (piezas que no pueden soldar por ambos lados) por ejemplo en tuberías en el cordón de fondeo y posiciones difíciles.
Son excelentes para soldar aceros con más del 0,25% de carbono y aceros efervescentes.
Base de Rutilo.- Se destacan por su tipo de acabado y facilidad de manejo su escoria se remueve fácilmente y en algunos casos sola. Su contenido de hidrógeno es alto y no requiere un proceso de exactitud.
El nombre del electrodo es propiamente incorrecto ya que el contenido de rutilo es principalmente un bióxido de titanio. Por este tipo de revestimiento se presta el electrodo para corregir fallas en el tipo de preparación.
Este electrodo se utiliza en trabajos de serie y de pocos requerimientos.
Bajo Hidrógeno.- Este tipo de electrodo produce las soldaduras de más alta calidad debido a su bajo contenido de carbono e hidrogeno. Como elementos componentes del revestimiento tiene:
Carbonato de Calcio.- Da una reacción básica a ¡a escoria, absorbe y neutraliza impurezas del azufre. Fluorita.- Neutraliza las impurezas del fósforo de tipo ácido que son perjudiciales. Manganeso.- Liga el azufre evitando los sulfuros y proporciona elasticidad a los depósitos.
Se utiliza este tipo de electrodos en aceros con alto contenido de carbono 0.25% aceros efervescentes y en construcción rígida.
Oxido de Fierro.- Este electrodo se caracteriza por su tipo de escoria liquida (propicia para soldar en vertical descendente) y su alta velocidad de deposito y limpieza.
Posee un alto contenido de manganeso como agente reductor y liga impurezas con la asistencia de silicatos formadores de escoria.
Polvo de Fierro.- Este electrodo contiene un 50% de fierro en el revestimiento, logrando hacer depósitos de 2.5 veces el alma del electrodo. Este electrodo. Fue hecho para competir con los procesos semiautomáticos en la industria, el tipo de electrodos más usados son el 7018, 7024, el primero en bajo hidrógeno y el segundo un parecido al 7014.
CLASIFICACIÓN DE LOS ELECTRODOS DE ACERO AL CARBÓN SEGÚN LA DESIGNACIÓN ISO
El sistema ISO de designación de los elementos de acero de bajo carbono es aproximadamente similar, o sea, nos proporciona las mismas informaciones del AWS, pero de la siguiente manera:
Ejemplo: ISO: E-51 4, B-120 26 H (corresponde a la clase. AWS E-7018)
E (Ref. "a") = La letra "E" encabeza al igual que la clasificación AWS. la designación del electrodo, y nos indica que el material de aporte es, electrodo ( véase el cuadro Características mecánicas.)
51 (Ref. "b") = quiere decir que pertenece al grupo "4" de los electrodos "51", con limite a la rotura de 510 - 610 N/Mm2 (véase cuadro características mecánicas).
4 (Ref. "c") =indica que pertenece al grupo "4" de los electrodos "51", con límite a la rotura de 510 - 610 N/mm2 , con un alargamiento mínimo de 20%, y una resistencia al impacto KV. min. de 352 , a una temperatura de ?300c. (Véase cuadro Características mecánicas).
B (Ref. "d") = se refiere a que este electrodo es del tipo con revestimiento básico (bajo hidrógeno) (véase cuadro Características mecánicas),
120 = se refiere al rendimiento del electrodo en %, en esté caso e¡ revestimiento produce aproximadamente un 120% . La designación del porcentaje del rendimiento se aplica para los electrodos con rendimiento se aplica para los electrodos con rendimiento del 110% en adelante.
26 (Ref. "E" y "F") = estos números nos proporcionan las características de aplicación referente a la posición de soldadura, tipo de corriente y polaridad, en la siguiente forma:
2 (Ref. "e") = se refiere a las posiciones de soldadura, en este caso el "2" nos indica que es apto para s posiciones excepto la posición e,
Soldadura Laser
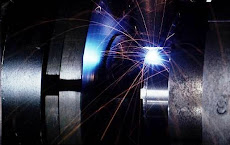
No hay comentarios:
Publicar un comentario